July 7th, 2020
We will describe Foundry by walking through the workflow for producing parts using Joule Printing™. All metal additive manufacturing processes follow the same basic steps, summarized in the figure below. (Refer to our blog on Metal AM Workflow). Core elements of Digital Alloys software power these steps. Data for integration with MES / ERP systems is also provided.
Design
A part design must conform with the design rules for the 3D printing process (see our blog on this topic). The most important rules for Joule Printing™ are:
- today the smallest printed feature is 3-5mm (smaller features can be machined into the part after printing); and
- the steepest overhanging feature that can be printed without support structures is 45 degrees.
Essential steps in the design are selecting parts that fit the AM process, identifying features that need to be added in the post-machining step, and identifying where supports will be needed.
An example part is shown below – a conformally cooled H13 steel tool for an automobile manufacturer. For H13 steel tooling, Joule Printing™ offers lower cost and faster turn-around than conventional machining. The part includes a conformal cooling channel that could not be manufactured conventionally. Minimal modifications were needed for this part. The customer selected a pre-existing part design (Joule Printing™ will be less expensive than conventional manufacturing), then added conformal cooling channels. The designer chose a diamond shape with tops that conform to the 45-degree overhang limit so that no supports are needed.
Joule Printing™, like most metal AM processes, is a near-net shape process. Printed parts have a surface roughness similar to a sand casting. Where smooth faces are required, extra material is added in a “near-net-shape expansion” – adding material that will be removed by finish machining during post-processing. For this part, 0.5mm of extra material was added on all sides.
In the future, Digital Alloys will add automated support generation and near-net-shape expansion to the Foundry Build Planner, the application dedicated to pre-processing.
Pre-Processing
Once the part design is complete, the CAD file is imported into Foundry’s Build Planner for pre-processing. Pre-processing converts a CAD file into instructions the printer uses to build each layer of the part. These instructions are created by a “slicer”, which automatically slices the design file into layers and generates a toolpath and process control parameters for the printing process. These instructions are described in g-code that tells the Joule Printer how to create the part. Digital Alloys uses a customized g-code protocol that will feel familiar to operators of other g-code-based 3D printers and CNC equipment. The Build Planner also provides the capability to simulate the part build.
We developed our own build planning solution because we could not find an off-the-shelf product that provided the control needed for optimal Joule Printing™. The Foundry Build Planner has unique, patented features which allow easy, interactive adjustment of the toolpath at every voxel, line, and layer of the part. These features also provide a platform for the future addition of algorithms that automatically optimize the Joule Printing g-code.
Printing
- Console UI dedicated for controlling printer operation,
- Real-Time Embedded Software that runs the Joule Printer, and
- Operations Manager for capturing data about a printer fleet:
- Printer configuration
- Print metadata
- Consumable usage and print-time statistics
The Console UI provides a user interface for interactively controlling and monitoring the printer. Our printers also include a web camera for recording and remote viewing.
The Real-Time Embedded Software is a hands-free firmware system that tightly controls key process parameters for every voxel in the part. This system includes control algorithms, device drivers, monitors, and an interface with our Console HMI.
Print Operations Management
The system captures and catalogues all process data, metadata, and print video for every print. The Operations Manager interface (Figure 5), is easy to navigate and search. It uses hyperlinks to connect to the background data and video for every print.
QA & Analysis
Post-Processing
- Smoothing of surfaces where the roughness of the printed part does not meet application requirements,
- Addition of fine features that are too small for Joule Printing, and
- Removal of support structures.
These steps are accomplished in a single finish machining operation. The part emerges from the printer welded to a base plate. Typically, the base plate is used to fixture the printed part in a CNC machine and provide reference marks for finish machining. After machining, the finished part is then cut from the plate.
For the finish machining steps, we use standard CAD/CAM tools to determine g-code for the CNC machining center. Notably, heat treatment is not usually required for most applications.
Conclusion
In our next blog post, we will provide a more detailed description of one of the software applications. Let us know what you’d like to hear about next by commenting in our social media threads or email us at [email protected].
Please check out other posts in our blog series:
Digital Alloys’ Guide to Metal Additive Manufacturing
Learn about the technology behind our process:
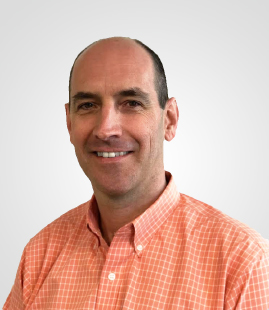
Duncan McCallum
CEO
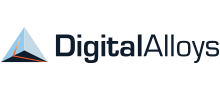
Digital Alloys is committed to providing the technology and expertise manufacturers need to use metal additive manufacturing in production — enabling them to save time, shrink costs, and produce valuable new product.